A Ferrari bemutatta az F80-at, egy szuperautót, amely jelentős előrelépés az erő, a forma és a technológia terén is. Az F80-at a 3D nyomtatási technológia integrálása is megkülönbözteti: ez az első alkalom, hogy a Ferrari additív gyártású (AM) szerkezeti elemeket alkalmaz egy közúti autójában.
Az F80 hibrid hajtáslánca lenyűgöző, 1200 lóerő, a 3 literes duplaturbós V6-os motort három elektromos motorral kombinálja. Míg természetesen nagy figyelmet fordítanak a gyorsulásra – mindössze 2,15 másodperc alatt 0-tól 100 km/óráig – a Ferrari fejlett gyártástechnológiáinak alkalmazása, beleértve a 3D nyomtatást is, az autógyártásban bekövetkezett fontos változást jelzi.
3D nyomtatott alkatrész - műszaki mérföldkő a Ferrari számára
A Ferrari fémnyomtatása alkalmazása kritikus alkatrészekhez a motorsportban szerzett tapasztalataira épít, különösen a Forma-1-ben. A kezdetben versenyautók számára fejlesztett technológiákat, ahol a teljesítményt finomhangolják, ma már beépítik az olyan közúti autókba, mint az F80. A Ferrari most először használt AM-et arra, hogy kritikus szerkezeti elemeket gyártson közúti járműveihez, kiemelve az F80 aktív felfüggesztési rendszerének felső lengőkarjait.
Ezek a felső keresztlengőkarok, amelyek hagyományosan összetett és súlyérzékeny alkatrészek, profitálnak a 3D nyomtatás által kínált pontosságból és rugalmasságból. Az AM használatával a Ferrari csökkenti a rugózatlan tömeget, optimalizálja a felfüggesztés geometriáját és javítja az általános kezelhetőséget és stabilitást. A technológia lehetővé teszi könnyebb, erősebb, bonyolult geometriájú alkatrészek létrehozását, amelyeket hagyományos módszerekkel nehéz, ha nem lehetetlen lenne megvalósítani. Ez javítja az aerodinamikát, a teljesítményt és a menetminőséget – ezek mind kulcsfontosságú jellemzői a 200 mérföld/óra sebességet meghaladó autóknak.
A 3D nyomtatott felső lengőkarok egy aktív felfüggesztési rendszer részét képezik, amely négy elektromos motort, kettős keresztlengőkaros elrendezést és aktív belső lengéscsillapítókat tartalmaz. A 3D nyomtatás integrálásával a Ferrari finomította a felfüggesztés elrendezését, megszüntette a bukókeretek szükségességét, és bevezette a dőlésszög-korrekciót, amely nagyobb pontosságot és reakcióképességet biztosít. Ez a rendszer megfelel annak a kettős követelménynek, hogy a pályán egyenletesen haladjon, miközben kényelmet és stabilitást biztosít az úton. Az F80 aktív aerodinamikai rendszerei további stabilitást biztosítanak erős fékezéskor és kanyarodáskor.
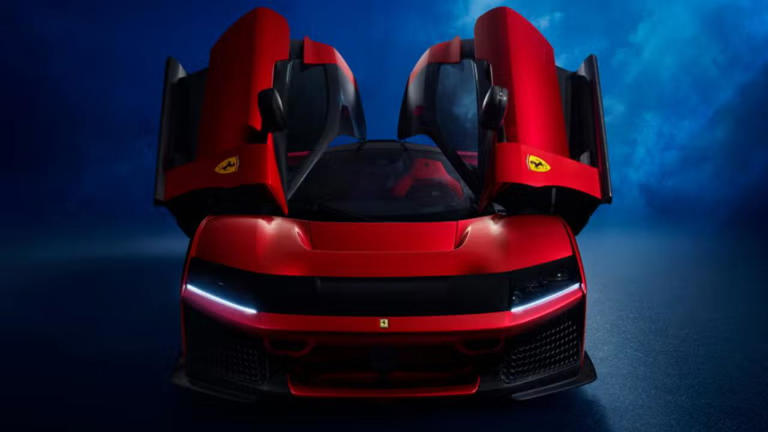
Az, hogy a Ferrari 3D nyomtatást használ az F80-ban, egy nagyobb tendencia az autóiparban, ahol a gyártók az additív gyártáshoz fordulnak könnyű, nagy szilárdságú alkatrészek gyártására. Egy olyan teljesítmény-orientált márka esetében, mint a Ferrari, minden megspórolt gramm és minden egyes ezredmásodperc, amelyet a gyorsulás során elért, mérhető különbséget jelenthet. A 3D nyomtatás által kínált precizitás és hatékonyság alapvető fontosságúvá válik ebben a törekvésben.
Ez a paradigmaváltás nem korlátozódik a Ferrarira. A Volkswagen például 2025-ig évente 100 000 alkatrész 3D nyomtatását tervezi. A BMW hasonló módon integrálta a 3D nyomtatást teljesen automatizált gyártósorokba, több ezer alkatrészt gyártva AM-mel. Más gyártók, mint például az Aston Martin a Valiant modellel, szintén bevezették a 3D nyomtatást a súly csökkentése és a kezelhetőség javítása érdekében.
Tanúi vagyunk az additív gyártás növekvő autóipari elfogadásának, amely a motorsportokkal kezdődött, majd kiterjedt a luxusautókra is, végül a fogyasztók egyre szélesebb körét célozza meg. Mindeközben a 3D nyomtatás gyártósori használata a történet kevésbé felkapott hírértékű hőse, hiszen a gyártásban már nagyon intenzíven használja a technológiátminden üzem. Míg a Ferrari F80-ból mindössze 799 darab készül majd, addig az autóiparban az a hosszútávú terv és tendencia, hogy több hétköznapi jármű végalkatrészeinek tömeggyártásához is használni fognak additív technológiákat.