A vasúti berendezéseket gyártó Wabtec a Nikon SLM Solutions fémnyomtatási technológiájának kiaknázásával javította áramszedőinek gyártását és teljesítményét.
A vállalat szerint ez az együttműködés jelentősen, 70%-kal csökkentette az alkatrészek tömegét és az életciklus költségeit, és 50%-kal csökkentette a gyártási időt. A Nikon SLM Solutions SLM 500-as gépének és az AM-ben szerzett széleskörű szakértelmének felhasználásával a Wabtec újratervezte az áramszedő felépítését, így több mint 17 különálló alkatrészt egyetlen, rendkívül hatékony komponensben egyesített.
Az AlSi fémporból készült új alkatrész kompakt kialakítással büszkélkedhet, amely javítja a rendszer általános megbízhatóságát, miközben jelentősen csökkenti a levegőszivárgás kockázatát; ez állandó probléma a hagyományos gyártási folyamatban. Ez az optimalizált kialakítás 30%-os teljesítménynövekedést is eredményezett, elsősorban a továbbfejlesztett légáramlás-szabályozás révén, ami hatékonyabbá tette az alkatrészt működési környezetében.
„Ez az együttműködés a Nikon SLM Solutions vállalattal lehetővé tette számunkra, hogy kitágítsuk a biztonság és a hatékonyság határait a vasúti közlekedésben. Az AM áramszedő automatikus leejtő eszközének innovációja és teljesítménye új szabvány lesz az iparágban” – mondta Henri de Chassey, a Wabtec Railway Transit alkalmazásainak 3D nyomtatási szakértője.
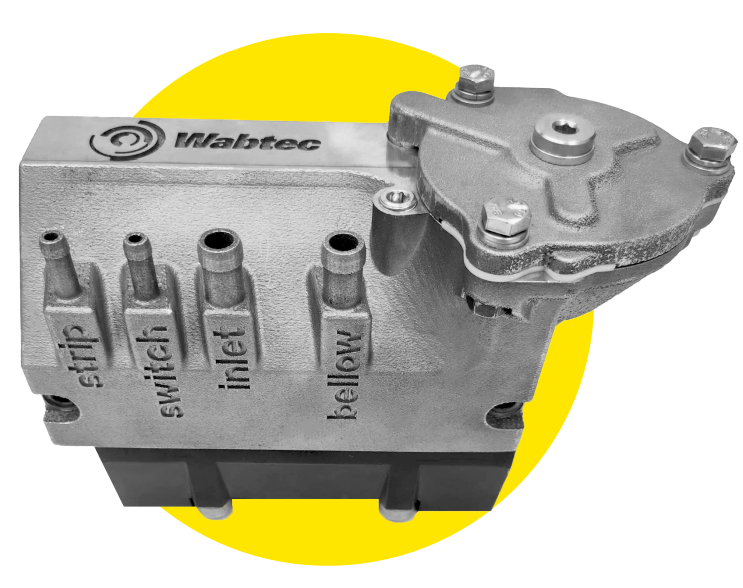
A Wabtec áramszedő automatikus leejtő eszközének 3D nyomtatott alkatrésze.
A Wabtec additív gyártás bevezetésére irányuló lépését az áramszedő berendezések hagyományos gyártási módszereivel kapcsolatos kihívások is befolyásolták. A hagyományos eljárás során olyan problémákkal szembesültek, mint a levegő szivárgása, a hosszabb forgalomba hozatali idő, valamint az alkatrészek összeszerelésének bonyolultsága, több beszállító bevonásával.
A fém 3D nyomtatás beépítésével a Wabtec csökkentette az alkatrész tömegét és gyártási idejét is. Ezenkívül az új kialakítás csökkentette a szükséges pótalkatrészek számát, így az ellátási lánc kezelését is. Az alkatrészek mennyiségének csökkenése az életciklus-költségek csökkenéséhez is hozzájárult, mivel csökkentette a karbantartási igényeket és megnövelte a tervezési rugalmasságot.
Az additív gyártásra való átállás azonban nem volt mentes a kihívásoktól. Kulcskérdés volt az újonnan tervezett komponensen belüli belső csatornák tisztítása, amely az alkatrész működőképességének biztosításához volt szükséges. Ennek kezelésére a Wabtec és a Nikon SLM Solutions speciális tisztítási eljárást fejlesztett ki.
Ezenkívül a csapat további tervezési kiigazításokat hajtott végre az alkatrész működése során fellépő lehetséges vibrációs problémák megoldása érdekében. Ezek az intézkedések fontosak voltak annak biztosításához, hogy az új nyomtatott alkatrész megfeleljen a Wabtec biztonsági és teljesítményszabványainak. A projekt során a Nikon SLM Solutions szakemberei technikai támogatást és útmutatást nyújtottak, hozzájárulva az újratervezett komponens fejlesztéséhez és megvalósításához.
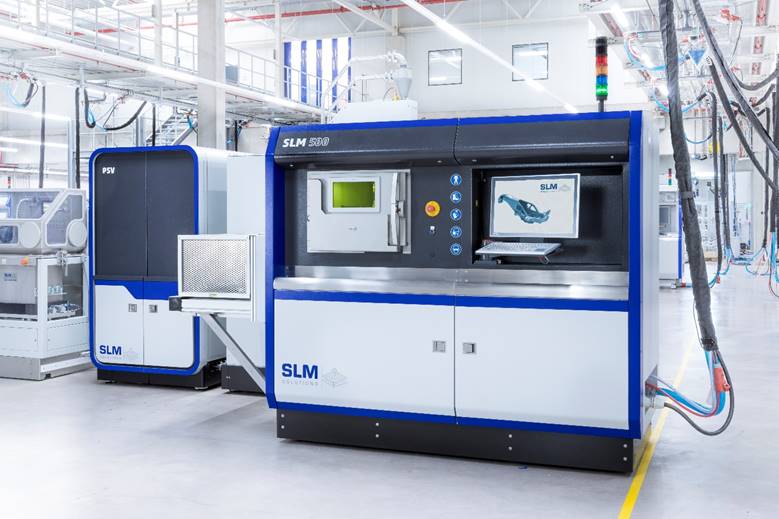
A Nikon SLM Solutions SLM500 3D nyomtatója
A vasúti ipar egyre jobban támaszkodik 3D nyomtatási technológiákra. A közelmúltban a Hitachi Rail ARGO 500 3D nyomtatókat vásárolt a Roboze-től, hogy fellendítse a prototípusok és pótalkatrészek gyártását a vasúti ágazatban. A nyomtatók nagy szilárdságú polimereket fognak használni, mint például az ULTEM 9085 és a Carbon PEEK, amelyek felváltják a hagyományos fémmegmunkálási módszereket a gyorsabb és költséghatékony gyártás érdekében. A fejlesztés célja az ellátási kihívások kezelése és a működési hatékonyság növelése a vasúti ágazatban.