A ONE3D egy Nikon SLM NXG XII 600E fémnyomtató rendszert szerzett be, hogy támogassa repülőgép- és védelmi ipari ügyfeleit fejlesztéseik megvalósításában.
A csehországi mohelnicei székhelyű ONE3D sro választása egy NXG 600E Laser Beam Powder Bed Fusion (PBF-LB) fémnyomtató rendszerre esett a Nikon SLM Solutions-tól. A beruházás várhatóan a cég repülőgépipari és honvédelmi ügyfeleivel folytatott munkáját fogja támogatni, beleértve a Lockheed Martin fejlesztési projektjét a cseh hadsereg F-35 vadászrepülőgép-programjában.
Ez az NXG 600E akár 600 x 600 x 1500 mm méretű fémalkatrészek gyártására képes, amelyhez nem kevesebb mint tizenkét darab 1 kW-os lézert használ. A ONE3D kijelentette, hogy az akvizíció összhangban van növekedési stratégiájával, lehetővé teszi a magas minőségű termelés bővítését.
Érdeklődik a fémnyomtató technológiák és rendszerek iránt? Töltse le fémnyomtatás útmutatónkat!
David Kadlčík, a ONE3D társalapítója megjegyezte: „A Nikon SLM Solutions technológiájának használata jelentős előrelépést jelent gyártásunk számára. Minden eddiginél nagyobb méretű, pontosabb és hatékonyabb összetett fémalkatrészeket tudunk majd létrehozni. Ez lehetővé teszi számunkra, hogy a terveket jobban igazítsuk az additív gyártás képességeihez, optimalizáljuk az anyag- és energiafelhasználást és csökkentsük az ötlettől a végtermékig eltelő időt. Egy ilyen tapasztalt partnerrel való együttműködés azt a magabiztosságot adja, hogy az iparági gyakorlatok élvonalában járunk. Bízom benne, hogy ezzel az új géppel képességeinket és versenyképességünket teljesen új szintre emeljük.”
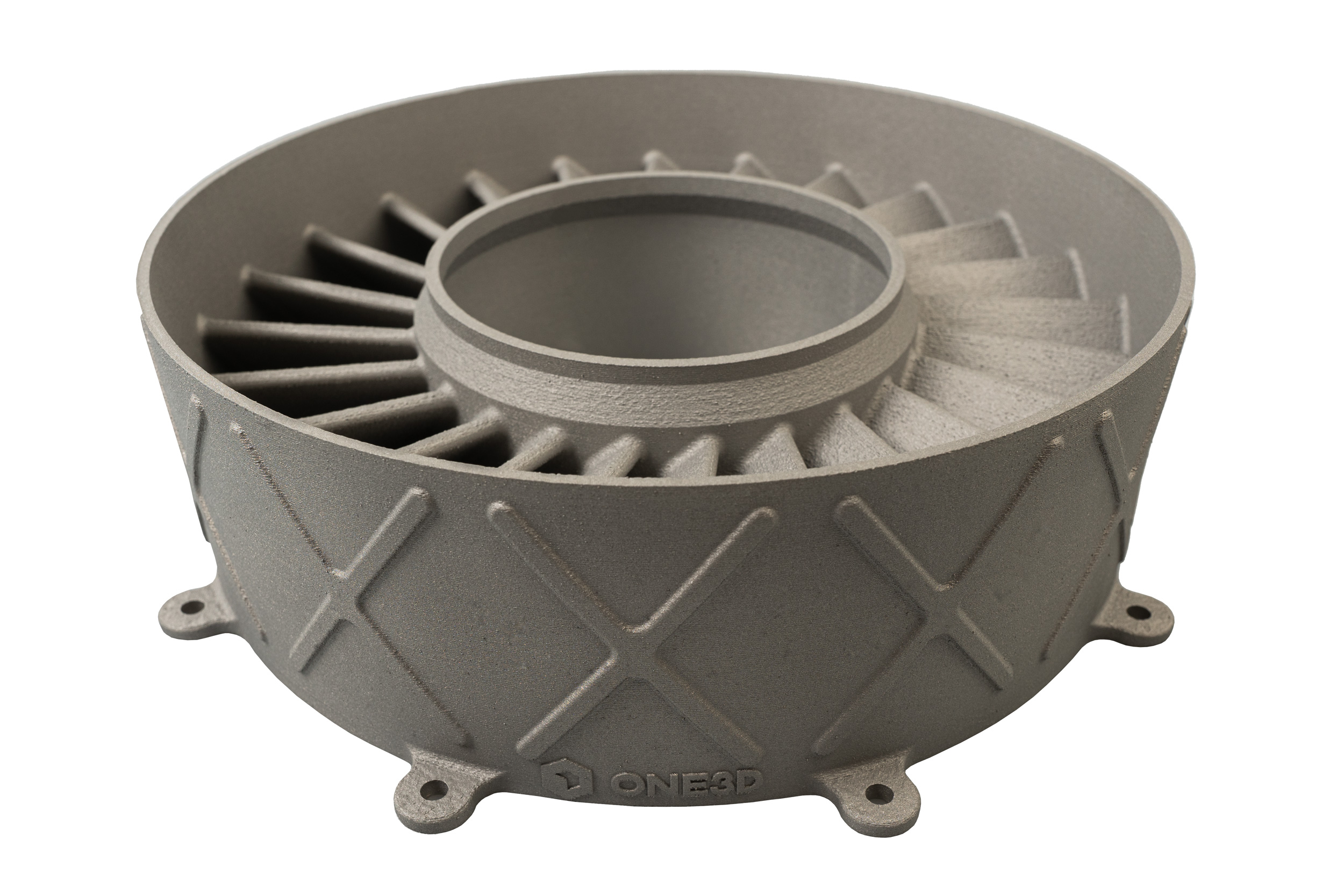
Kép forrása: one3d.cz
Sam O'Leary, a Nikon SLM Solutions vezérigazgatója így nyilatkozott: „Nagyon örülünk, hogy támogathatjuk a ONE3D-t a fejlett, nagy léptékű additív gyártás felé vezető úton. Az NXG 600E-t úgy tervezték, hogy megfeleljen a nagy teljesítményű iparágak legszigorúbb követelményeinek, és képességeivel az ONE3D készen áll arra, hogy új mércét állítson fel a precizitás, a termelékenység és az innováció terén. Kíváncsian várjuk, hogyan hasznosítják technológiánkat a határok feszegetésére és transzformatív eredmények elérésére repülőgép- és védelmi ipari ügyfeleik számára.”
Több mint egy évtizedes tapasztalata során a ONE3D K+F részlege vezető vállalatokkal és kutatóintézetekkel működött együtt. Elnyerte az ISO 9001, ISO 14001 és ISO 45001 tanúsítványokat, és jelenleg az AS9100 minősítést célozta meg.
Az úttörő Nikon SLM Solutions fémnyomtatókat Magyarországon a FreeDee Kft. forgalmazza.